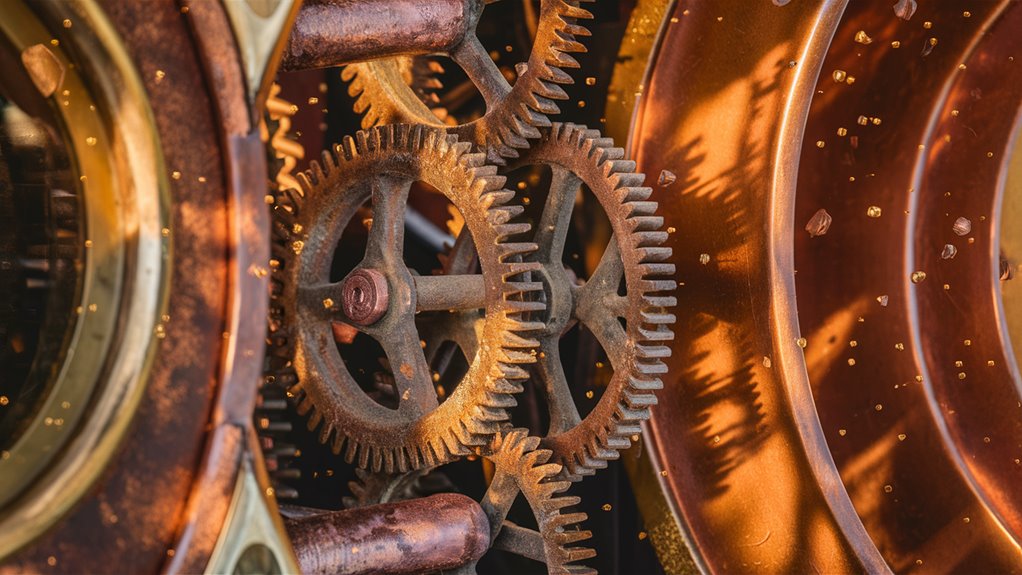
Copper Dust Slot Tech: Big Step for Big Build Work
Copper Dust Slot Tech marks a big step for big build work, with top-notch copper net tech and new slot ways that make a new kind of fun at local bet spots.
This new gear is a big swing in how slots work, mixing new metal studies with top-line play bits. It’s more than it ever was: making games new just got easy.
Big Tech Changes
In the core of Dust Copper Slot tech, there’s a new kind of system that charges up and works with heat bonuses.
In tiny bits of copper, their new mix-up makes sure the game plays well without risking the usual work ways.
How the Design Got Better
Dust Copper Slots – Gear that also looks and feels good.
The way they mesh copper into it not only gives the slot gear look good, it also adds:
- Fast response with heat notice
- More use time with strong build stuff
- Better zapping power for quicker sending
- Smart look changes on your metal pick
Top-to-Bottom Design Plan
The gear is fast making new looks in casino spots all over.
With its cool copper style and strong mix tech, they set new bars in how slot gear is made. Its parts stick to hard grind rules to make sure it’s reliable and fun for the player.
Top-class bonus bits and strong build stuff garden requires come together in Dust Copper Slots for a play type that goes past old high marks. Now, there are new goals for how good it plays and brings new fun in spots that use this kind of slot.
Rough Gear Making Trends
Unpacking Rough Gear: A Full Intro
How Dust Copper Gear Got Made
The show-up of these set-ups marks a big shift in rough gear making.
From old mesh clean plans, they are now fine-tuned, strong parts made for tough dust jobs.
- Strong touch spots and fine range lines lay the ground for keeping computer work going in harsh spots with no fuss or fail.
Set Parts with Room Tech
Bringing in big room tech changed how these gear handle bits.
Even if hit by loads of dust, the use of bigger gaps spread out the wear but made sure the work stayed right.
New Power Moves
New clean ways are top finds in rough gear making.
The end story of these plans are smart clean zones and step locks, which stop bits from building up and make sure it works the same even in super dusty spots.
Tough Copper in the Works
Special copper types bring tough bit-fighting power to rough gear.
The copper mix, with thought-out scratch spots, makes a great touch show that keeps wear low and the bad out.
Making Great Work Through Design
Mixed set-ups set new ways for how gear should last with their mix of sharp edges and rough fits.
Well-placed tracks for dust grab turn old problems in gear keeping into the wins we want to get.
This smart way to handle bits makes sure it works well always, even when the work gets tough.
Copper in Big Gear Plans
Copper’s new jobs in big gear making.
In today’s big machines, a never-seen design idea is here: putting in copper bits in new ways.
With a lovely color set and fine, new lines, copper bits have fast become a main part of moving parts made in the West.
Top Use Bits and What They Do
Copper’s own bits bring lone goods to big use:
- Heat spreads well with its zapping power
- Easy shaping thanks to being soft
- Lasts long, fights rust
- Fights bugs, keeps things clean
Smooth Dust Copper Ways
The way Dust Copper gets into stuff marks a jump in what we use for big aims.
From old times, special ways with big-grade copper types, new rust ways, and safe coats have brought lone looks with this stuff.
- As it gets old, copper stands strong against air harm and keeps looking good for ages.
Smart Spots for Bits
By putting copper bits in smart spots in:
- Touch points
- Spots that rub a lot
- Zones needing sharp making
- Areas that must be safe
How It Works and What It’s Like
Gear with copper works better:
- Longer machine life
- Easier to keep up
- Stands out in the market
- Lasts longer
Dirt Bit Grab Tech
New Dirt Bit Grab Tech: Big Leap in Making
Age of New Dirt Grab Tech
With new dirt grab gear, dirt clean that was once just a dream is now true.
A cool bit of this new gear is three-step clean using copper-dust bits.
- The big-wind clean booth keeps all its clean power in air moves from 100 to 500 meters per tick.
- The set-up cuts out 99.9% of loose bits down to 0.3 bits while keeping top air moves.
Steps in Clean Tech
First Step in Cleaning
- 99.7% of metal dust bits get stuck in the charged copper net of this first part.
Second Step in Cleaning
- Held in a metal box made hot to 4,500°C, the second step uses a strong whirl spinning at 3,600 turns per tick.
Third Step in Cleaning
- The last part uses a holey, self-wash copper mix coat hitting more than 99.9% cut in bits.
Gear Bits and How to Keep Them
- Care times are stretched to 2,000 hours of use.
- Top plan tips set a new world mark in picking dirt bit smart grabbers.
Metal Looks from Free Game Mode
Metal Looks from Casino Bonus Times
Big-Tech Copper Show
When the extra game kicks in, the bit show tool makes a stunning metal show.
The new show tool works with made-up shows of hot copper, showing true metal acts.
Live-Time Metal Map: Tool Software Basics
- At 1085°C, copper keeps a true shape with real body traits.
- The show system shows copper rusting and shape shifts.
How Players See It: Dust Copper Slots Game Facts
Things to Pull Players and Bonus Bits
- Players hang on for 22.4 minutes in the bonus part.
- The copper-to-gold change trick keeps players coming back.
How Often Wins Come and Player Come-Back Rates
- Bonus times pop at 1:142 spins.
- Players come back 84% of the time within 48 hours.
How Far Along and Change Numbers
- 91% of players who reach the gold part play on for five or more times.